The first step in surface preparation is degreasing- - removal of grease and other contaminants of various origin from the surface of the aluminium. The surface thus cleansed is subjected to digestion- alkaline bath phase – removal of oxide layer from product surface, giving it a matt finish and to compensate for minor defects after stamping or rolling, such as streaks, thermal belts and delicate scratches. The alternative finish of satin surfaces is chemical brightening. By acidifying a mixture of concentrated acids, the surface structure is smoothed out, which significantly reduces matting and brightens the surface of the metal and results in a glossy finish.
These operations are carried out in special baths and each process requires separate. Between the essential processes the rinsing operation of the product is performed.
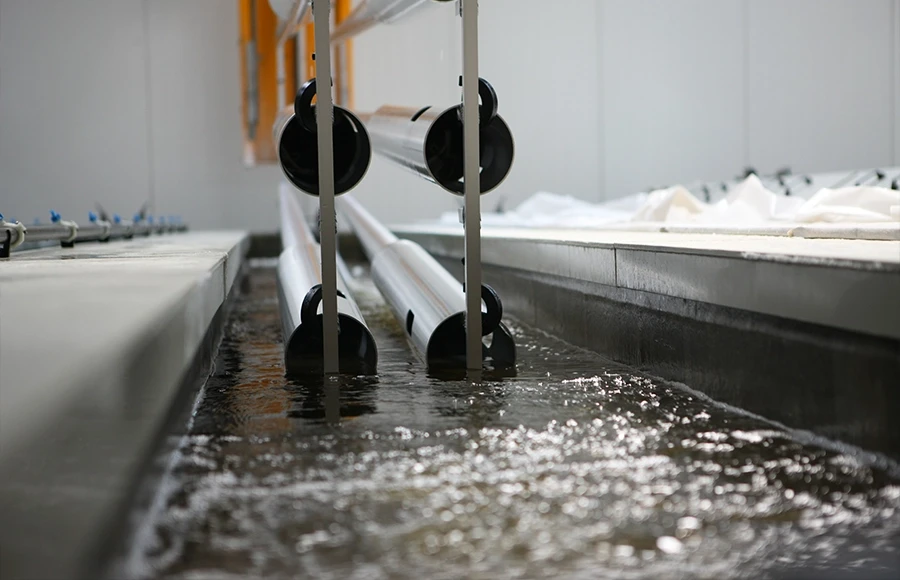
Next process of preparing the surfaces for anodising is lightening (pickling) –finally remove the thin oxide layers and deposits that may have remained after satin etching or lightening, and which removal is necessary to achieve a uniformly structured oxide coating.
Anodising is the electrochemical formation of aluminium oxide on the surface of aluminium. This coating is made in aqueous sulfuric acid, and the anodised element performs an anode function in this process. During electrolysis, when oxygen is applied to the anode at a specific density, oxygen is released and reacting with the metal forming a transparent oxide coating. The coating thus formed grows in 2/3 of its thickness into the metal surface and grows 1/3 above it. It is much thicker than natural, so it effectively protects aluminium from further oxidation, i.e. corrosion. Its porous structure also allows for permanent colouring of the product by electrochemical or interference method with high UV resistance.
Electrochemical colouring is based on the treatment of the anodised product in the electrolyte containing tin ions. Reduced in a cathode cycle metal is de-posited on the bottom of the pores of the oxide coating and gives a permanent colouring to the aluminium surface. This results in a range of colours from bright to dark shades of brown and black.
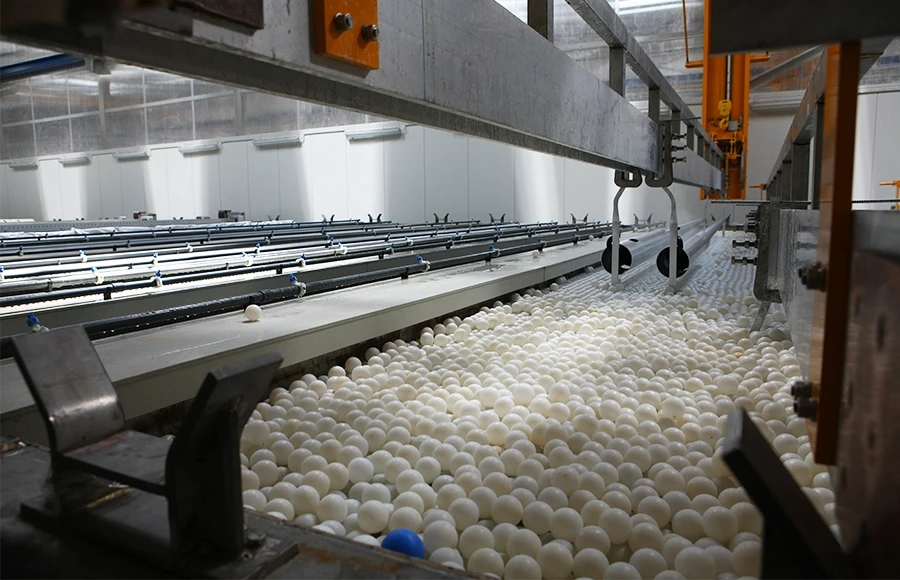
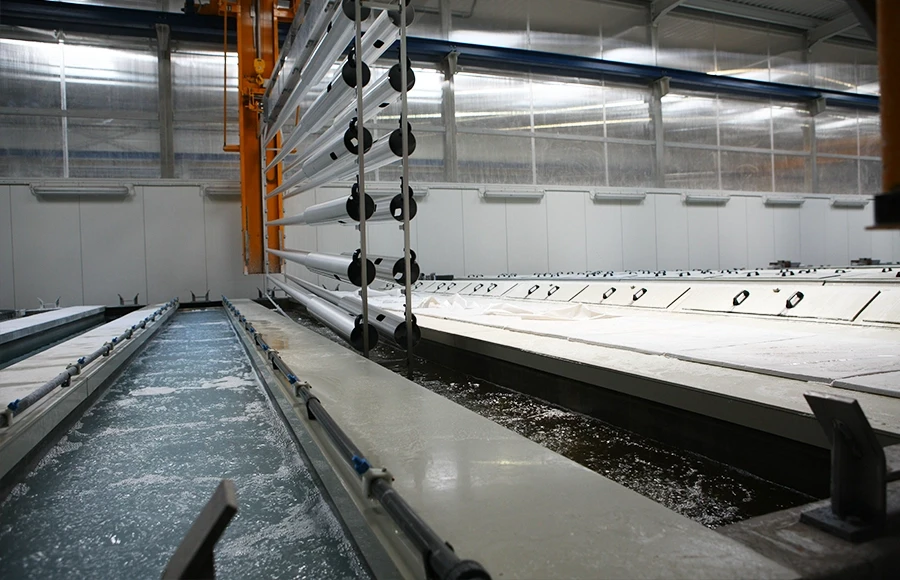
Interference colouring is preceded by pore shape modification operation of the anodic layer. At this stage, the structure of the lower part of the porous layer is changed by giving it a spherical shape. Such modified layer is subjected to an electrochemical colouring, in tin-based baths, widening the colour palette of electrochemical colours with gray and green shades. This method uses the phenomenon of interference, that is, the overlapping of reflected light waves, leading to the increase or decrease of the amplitude of the incident wave. Modifying this amplitude through the appropriate controlled variation of the pore shape of the anode layer allows for an appropriate optical effect (colour).
The last step in anodised technology is sealing consisting of closing the porous oxide layer. The medium temperature seal (86-88 °C) is used to immerse the product in hot demineralized water with accelerating additives to fill the pores of oxide layer with boehmite. Thanks to sealing, the anodised surface becomes sealed and smooth, which makes the oxide coating resistant to atmospheric corrosion and reduces the tendency for sedimentation on the product surface.
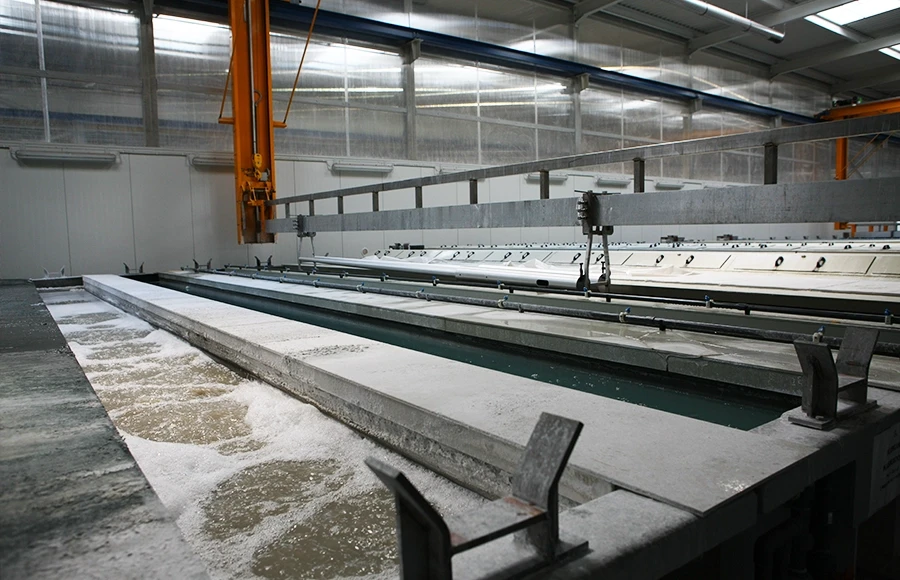
Proper maintenance and regular cleaning of anodised aluminium products keep their aesthetic and decorative appearance for longer. From 2017 the plant also uses technology so-called dry etching involves surface treatment by shot blasting method. The process is carried out using a modern machine to matt the surface by subjecting the workpieces to abrasive blasting operations using shot with a diameter of about 0,1 mm, giving the surfaces a delicate, satin appearance. This type of technology allows to significantly eliminate all kinds of surface defects arising from extrusion or rolling processes such as streaks, thermal lines, etc. and minor mechanical damages in the form of scratches and abrasions. The surfaces thus obtained are characterized by much better quality compared to traditional chemical etching. Used technical solutions allow to shot blast elements from sheet thickness of 1mm without the risk of surface damage.