La prima fase della preparazione della superficie è la sgrassatura. Consiste nella rimozione di oli e loro derivati dalla superficie dell'alluminio nonché di eventuali impurità originate dalla lavorazione meccanica dei pezzi. La superficie ripulita viene quindi sottoposta ad una satinatura alcalina che ha lo scopo di rimuovere lo strato di ossido intrinseco dalla superficie del manufatto e di conferire alla superficie un aspetto uniformemente opaco nonché di eliminare piccoli difetti dopo il processo di pressatura o laminazione, come striature, strisce termiche e piccoli graffi. Grazie alla mordenzatura in una miscela di acidi concentrati, la struttura della superficie viene levigata, riducendo significativamente l'ossidazione e ravvivando la superficie metallica conferendole un effetto lucido.
Queste operazioni vengono eseguite in bagni speciali. Ciascun bagno richiede un processo separato e tra i singoli processi chimici vengono eseguite le cosiddette operazioni di risciacquo del prodotto.
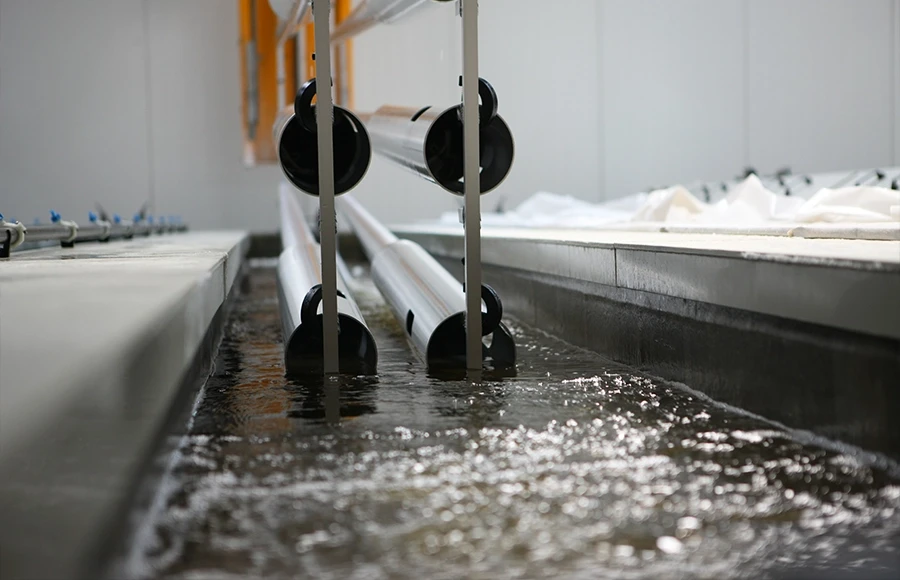
La successiva fase di preparazione della superficie per l'anodizzazione è la brillantatura (decapaggio), il cui scopo è la rimozione finale di sottili strati di ossido e depositi che possono essere rimasti dopo i processi di satinatura e la cui rimozione è necessaria per ottenere un aspetto strutturalmente uniforme rivestimento di ossido.
L'anodizzazione comporta la formazione elettrochimica di un sottile strato di ossido di alluminio sulla superficie di alluminio. Questo strato viene prodotto in una soluzione acquosa di acido solforico e il componente anodizzato funge da anodo in questo processo. Durante l'elettrolisi, quando all'anodo viene applicata una tensione continua di una certa densità, viene rilasciato ossigeno, che reagisce con il metallo formando un rivestimento di ossido trasparente. Il rivestimento così prodotto cresce per 2/3 del suo spessore nella superficie metallica e per 1/3 sopra di essa. È notevolmente più spesso del rivestimento naturale e quindi protegge efficacemente l'alluminio da un'ulteriore ossidazione, ad esempio la corrosione. Inoltre, la sua struttura porosa permette al prodotto di essere colorato in modo permanente mediante metodi elettrochimici o di interferenza, conferendogli un colore altamente resistente ai raggi UV.
La colorazione elettrochimica prevede il trattamento del prodotto anodizzato in un elettrolita contenente ioni di sale di stagno. Il metallo ridotto in un ciclo catodico si deposita sul fondo dei pori del film di ossido, conferendo una colorazione permanente alla superficie dell'alluminio. Questo produce una gamma di colori dal marrone chiaro al marrone scuro fino al nero.
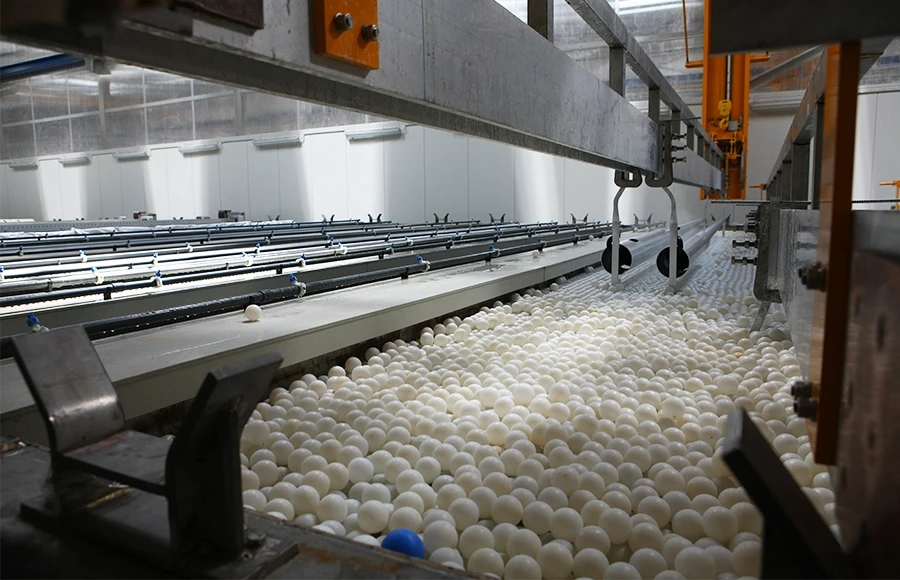
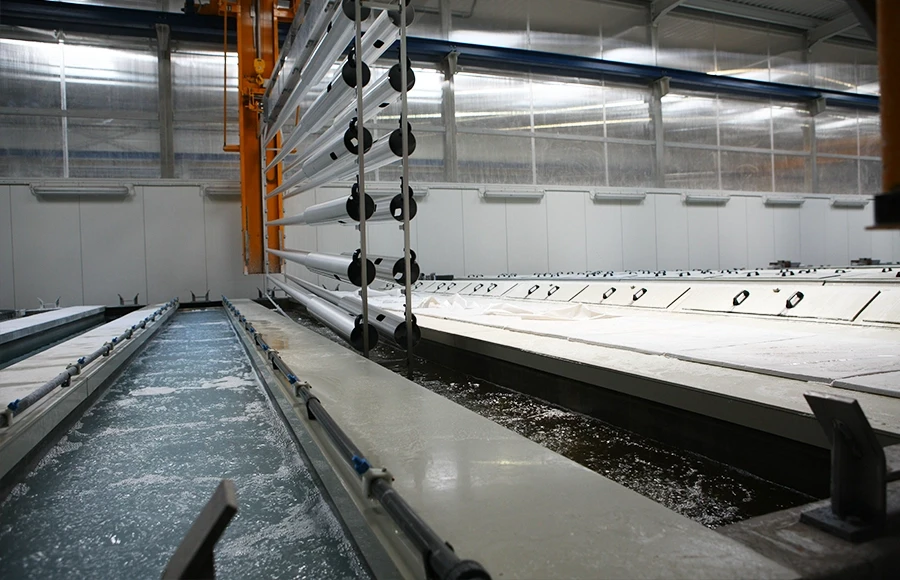
La colorazione ad interferenza è preceduta da un'operazione di modifica della forma dei pori del rivestimento anodico. In questa fase la struttura della parte inferiore dello strato poroso viene modificata conferendogli una forma sferica. Lo strato modificato viene quindi sottoposto a tintura elettrochimica in bagni di sale di stagno, estendendo così la tavolozza dei colori ottenuta nella tradizionale tintura elettrochimica fino a includere sfumature di grigio e verde. Il metodo sfrutta il fenomeno dell'interferenza: la sovrapposizione di onde luminose riflesse, che porta a un aumento o ad una diminuzione dell'ampiezza dell'onda risultante. Modificando tale ampiezza attraverso un cambiamento opportunamente controllato della forma dei pori dello strato anodico, è possibile ottenere un opportuno effetto ottico (colore).
Il passaggio finale nella tecnologia dell'anodizzazione è il fissaggio. Questo si basa sulla sigillatura della struttura di ossido poroso. La sigillatura a media temperatura utilizzata (86-88°C) viene effettuata immergendo il prodotto in acqua calda demineralizzata con additivi acceleranti. Lo scopo di questa azione è riempire i pori della superficie dell'ossido con boehmite. Grazie al fissaggio, la superficie del componente anodizzato diventa tesa e liscia, rendendo il rivestimento di ossido resistente alla corrosione atmosferica e meno soggetto alla deposizione di contaminanti sulla superficie del prodotto.
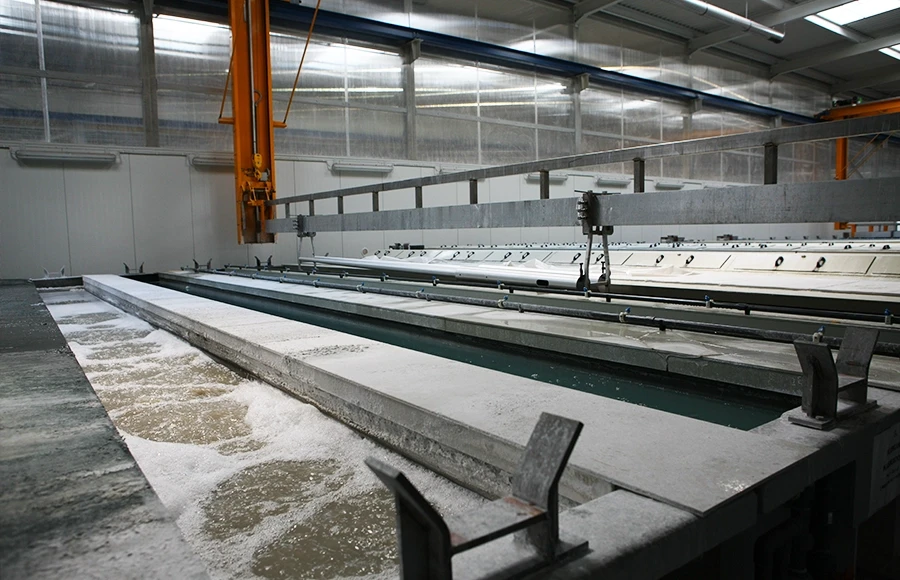
Per mantenere le qualità estetiche, i prodotti in alluminio anodizzato devono essere puliti e mantenuti periodicamente.
Dal 2017 l'impianto utilizza anche la cosiddetta tecnologia dry etching che consiste nel trattamento superficiale mediante granigliatura. Questo processo viene eseguito utilizzando una macchina per opacizzazione superficiale all'avanguardia, sottoponendo i pezzi in lavorazione a sabbiatura abrasiva, utilizzando sfere con un diametro di circa 0,1 mm. Il risultato è una superficie dall'aspetto fine e satinato. Questo tipo di tecnologia consente di eliminare in modo significativo tutti i tipi di difetti superficiali, come striature, strisce termiche, ecc., nonché piccoli danni meccanici sotto forma di graffi e grippaggi, derivanti dai processi di estrusione o laminazione. Le superfici così ottenute sono caratterizzate da una qualità decisamente migliore rispetto alla tradizionale incisione chimica. Le soluzioni tecniche applicate consentono la granigliatura di componenti in lamiera a partire da 1 mm di spessore, senza il rischio di danneggiarne la superficie.
Dal 2017 l'impianto utilizza anche la cosiddetta tecnologia dry etching che consiste nel trattamento superficiale mediante granigliatura. Questo processo viene eseguito utilizzando una macchina per opacizzazione superficiale all'avanguardia, sottoponendo i pezzi in lavorazione a sabbiatura abrasiva, utilizzando sfere con un diametro di circa 0,1 mm. Il risultato è una superficie dall'aspetto fine e satinato. Questo tipo di tecnologia consente di eliminare in modo significativo tutti i tipi di difetti superficiali, come striature, strisce termiche, ecc., nonché piccoli danni meccanici sotto forma di graffi e grippaggi, derivanti dai processi di estrusione o laminazione. Le superfici così ottenute sono caratterizzate da una qualità decisamente migliore rispetto alla tradizionale incisione chimica. Le soluzioni tecniche applicate consentono la granigliatura di componenti in lamiera a partire da 1 mm di spessore, senza il rischio di danneggiarne la superficie.